 |

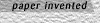
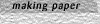
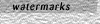
 |
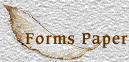
The art of making
business forms commences at the pulp mill as clean bleached pulp of cellulose fibres
is produced out of timber. A lot of consideration is generated towards the combination
of fibres in order to attain high opacity, good print results, strengths and runability.
The choice of materials varies with geographic location of the mill.
Business forms are crafted out of a continuous
process which involves a stretch of process beginning
from the headbox right up to the reel. Prior to feeding the pulp into the headbox
of the paper machine, it is mixed with filler, starch, additives with plenty dosage
of water. From the headbox, the fed is uniformly distributed on the wire where most
of the water content is drained away. This process continues in the drying section
through the press section where more water is quenched out. Once this is completed,
the surface is sized with starch as to prevent linting. The last stage involves the
calendering of the paper wounded to the requested reel sizes and delivered to the
form producers.
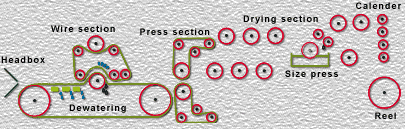
The noble art of forms paper making
Alternative form papers have been developed
to save cost and as a mean to protect the environment. More is done to reduce waste
by recycling used papers which consists of a mixture of fibres with different materials.
Bleached chemical pulp contributes to the woodfree paper used widely in business
forms making.
To achieve excellent prints on business forms,
manufacturers used clay and chalk as a coating
on its surface. This is especially done for certain exclusive forms or direct mails.
Moisture and temperature
plays a great role in business forms making because a slight difference can contribute
towards swelling and shrinking of paper, static electricity, wavy edges, tight edges,
curls, folding problems in printers and many more.
Papers should normally be produced with a moisture
content corresponding to a relative humidity of about 50%, and then moisture proof
wrapped. Different level of moisture content is required by different printers. A
less dry paper will definitely shrink due to significant rise in temperature as the
paper passes through a laser printer.
Static electricity in business forms normally
shows up due to excessive dry paper and air in the print room combined with too high
paper resistivity. This causes the paper hard to fold and sticking to one another.
Another common problem which arises when the
temperature becomes unstable is wavy edges. Despite the enlargement of the edges,
the centre retains its original dimensions when the paper is exposed to air with
high relative humidity. Changes of humidity makes the fibres swell.
Dry atmosphere makes the edges of a paper to
tighten when the moisture nearest to it gets released while the centre still in its
original dimensions.
An unwrapped sheet of paper left exposed to dry
air or that undergoes a significant rise in temperature in laser printer will develop
a curl. This in the end makes printing job tougher as one encounters problem feeding
them in the printers.
|
|